Ce site utilise des cookies afin que nous puissions vous fournir la meilleure expérience utilisateur possible. Les informations sur les cookies sont stockées dans votre navigateur et remplissent des fonctions telles que vous reconnaître lorsque vous revenez sur notre site Web et aider notre équipe à comprendre les sections du site que vous trouvez les plus intéressantes et utiles.
Peut-on souder de l’aluminium avec la machine à souder au laser ?
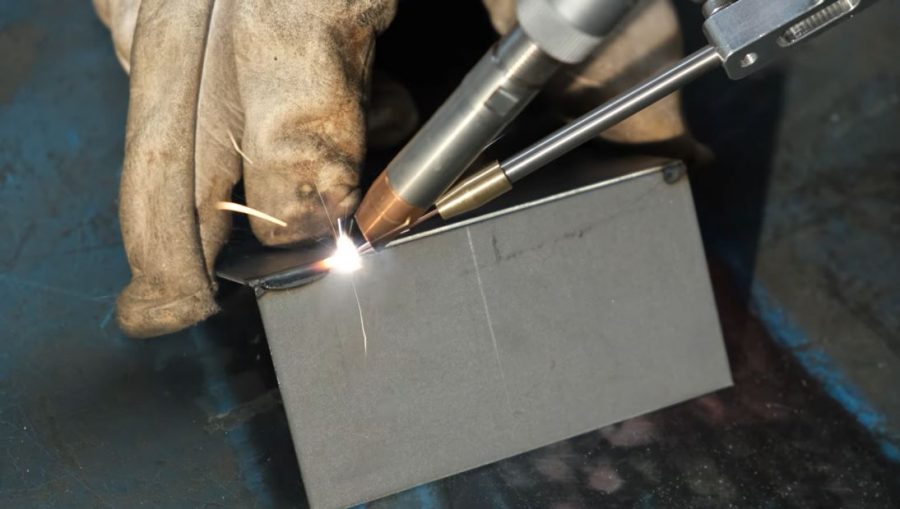
Résumé :
L'aluminium est un métal très léger qui présente des propriétés intéressantes et de grands avantages : c'est un très bon conducteur d'électricité et il offre une grande résistance à la corrosion. Le soudage de l'aluminium à l'aide de techniques traditionnelles telles que le TIG, le MIG ou le MAG est un grand défi, même pour les soudeurs expérimentés.
LC-WELD de LC Lasers facilite ce processus et permet d'obtenir de meilleurs résultats. Le soudage au laser permet de souder tous les métaux avec une précision et une résistance étonnantes. Tout cela sans avoir besoin d'une grande expérience préalable, car il est très facile à utiliser. L'aluminium peut être soudé avec ou sans produit d'apport, comme dans la vidéo.
Grâce à la soudure au laser, nous pouvons surmonter la barrière de l'expérience et les complications que présentent certains métaux, en obtenant un résultat esthétique et résistant grâce à une méthode simple, pratique et rapide.
Une soudure solide, exempte de fissures.
Le soudage au laser est un système innovant, qui est devenu l'option numéro un dans le secteur. En raison du grand nombre d'avantages qu'il peut nous apporter.
La soudeuse laser LC nous permet de réaliser des soudures résistantes et de haute qualité sur différentes surfaces et types de joints. En travaillant à une vitesse plus élevée, cela nous permet de réduire les coûts et d'améliorer l'efficacité. Comme dans certains cas, être capable d'éliminer le besoin d'un polissage ultérieur.Dans ce cas, on utilisera le LC-WELD pour souder un métal léger comme l'aluminium.
Démonstration de l'efficacité du soudage laser. Si avec l'aluminium, qui est en soi un métal très délicat, nous obtenons des résultats efficaces en peu de temps. Avec le reste des métaux, vous aurez toujours des résultats de meilleure qualité.
Soudage au laser par rapport à d'autres systèmes alternatifs.
Grâce au soudage laser, nous pouvons accéder à une série d'avantages par rapport à d'autres méthodes alternatives telles que le soudage TIG ou TAG. Ensuite, nous décrirons les principaux avantages qui placent le soudage au laser comme l'option principale lors du choix entre une option ou une autre.
- Précision et qualité : Le soudage au laser permet une grande précision dans l'assemblage des matériaux. Le faisceau laser focalisé permet un contrôle précis de la quantité d'énergie appliquée, résultant en des soudures de haute qualité avec une zone affectée par la chaleur plus petite. Il en résulte des joints plus propres, avec moins de distorsion et moins de risques de défauts.
- Rapidité et productivité : Le soudage au laser est un processus rapide par rapport aux autres méthodes de soudage. La densité d'énergie élevée du laser permet une fusion et une solidification rapides des matériaux, ce qui réduit les cycles de soudage. Cela améliore la productivité et l'efficacité de la ligne de production.
- Polyvalence des matériaux : le soudage au laser peut assembler une grande variété de matériaux, notamment les métaux, les plastiques, la céramique et le verre. Cela permet des applications dans différentes industries, de l'automobile et de l'aérospatiale à l'électronique et au médical.
- Contrôle de la zone affectée thermiquement : Le soudage au laser génère une zone affectée thermiquement très petite et contrôlée. Cela minimise les dommages thermiques aux matériaux environnants, ce qui est particulièrement important dans les applications où une haute précision est requise et pour éviter les déformations ou les dommages.
- Soudage sans contact : Lors du soudage au laser, le faisceau laser est focalisé et dirigé vers la zone de joint sans contact physique avec les matériaux. Cela évite l'usure et la contamination qui peuvent se produire avec d'autres méthodes de soudage nécessitant un contact direct.
- Soudage dans des zones difficiles d'accès : grâce à la flexibilité du faisceau laser, le soudage au laser peut atteindre des zones difficiles d'accès, telles que des joints étroits ou des espaces confinés. Cela vous permet de souder des composants qui seraient difficiles à atteindre avec d'autres méthodes de soudage.
- Déformation minimale : Le soudage au laser produit moins de distorsion et de déformation par rapport aux autres méthodes de soudage. Le taux élevé de chauffage et de refroidissement réduit l'effet de la dilatation thermique, aidant à maintenir la forme et les dimensions d'origine des pièces soudées.