This website uses cookies so that we can provide you with the best user experience possible. Cookie information is stored in your browser and performs functions such as recognising you when you return to our website and helping our team to understand which sections of the website you find most interesting and useful.
Can we weld aluminum with the laser method?
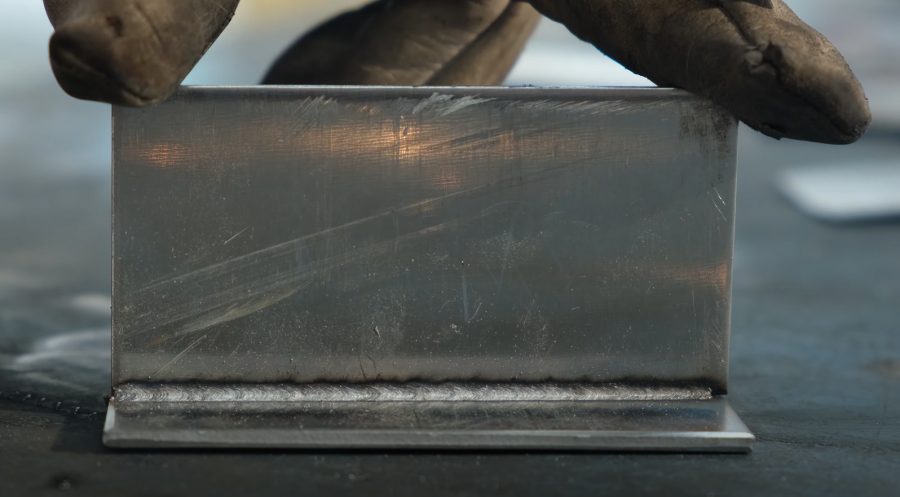
Summary:
Aluminum welding is a process that, carried out with traditional welding methods (TIG and MIG among others) is quite difficult to carry out.There are several materials that without previous experience it is difficult to weld. And this happens with materials such as aluminum. At first it may seem that this material is easier than other metals. But it is not true, to weld this material great precision is needed to achieve a solid union between both pieces.
But this changes with LASER WELDING . LaserComercial LC-WELD laser welding equipment allows welding all metals with amazing precision and resistance. All this without requiring a great deal of previous experience since it is very easy to use.
This laser beam technique is the latest innovation in welding. We are going to know in detail why laser welding is suitable and recommended to easily weld aluminum.
Complications of welding aluminum with methods other than laser
The use of aluminum for the manufacture of various products is very common in various industries. The aluminum is insulated by a tough, oxidized layer.
This material is very sensitive to dirt, and it is difficult to weld because it tends to bubble and lose strength when overheated. It is also a difficult material to weld properly due to its very high thermal conductivity and its low melting point, which makes it easily deformable. Some welding methods generate a lot of heat, which can quickly deform the aluminum material and the product. Aluminum is covered by an oxide film, which creates additional processing difficulties because the oxide film melts at different temperatures than aluminum itself . The possibilities and technologies for welding aluminum are very limited compared to other materials.
On the other hand, aluminum welding involves working with different types of thicknesses, so welders must know how to work with each of them.
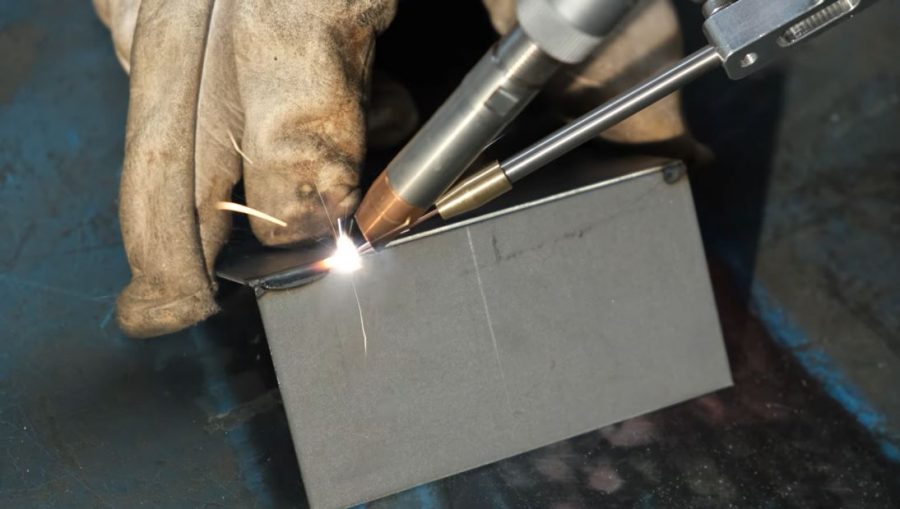
Laser welding applied to aluminum
Laser welding is a faster and easier process than other welding techniques . This equipment can produce tight, concrete welds, but with a lot of depth, less heat penetrates into the material, so no warping occurs. Power levels like 1500W and 2000W allow for greater depth in our welds and achieve a stable keyhole weld.
Another factor that convinces many users regarding laser welding is the speed at which we can work. With laser welding, the welder decides what speed to work at and sets the machine to match their speed.
With this welding technique, we do not need to polish afterwards and it does not leave welding marks. The LC-WELD can choose to work with the addition of material or without it, depending on the finish and welding that we want to achieve. The addition of material in laser welding can be very suitable to reduce the cracking that would occur in some thicknesses of aluminum plates.
In short, laser welding machines allow minimal heat input to the material, a very specific and narrow weld bead, high speeds and a lot of depth if required.
Laser welders can also successfully weld other materials such as stainless steel, carbon steel, galvanized steel, titanium, and brass. These are extremely versatile machines that can make work easier in many fields and sectors.
Benefits of LC-WELD compared to traditional methods:
Laser welders, as we have already mentioned, have many advantages to achieve good results in each job. It is an application of laser technology that is gaining popularity, mainly because it offers us numerous advantages to achieve better welds and resistant structures. We can make precise and deep welds if desired, all without losing strength and weld quality. We are going to know in detail what laser welding offers us.
Save time and costs. Laser welding allows to reduce the subsequent polishing process, thus avoiding extra costs and time. In addition, laser welding equipment has a long service life and few consumables.
Less experience and ease of operation. Another characteristic of laser welding machines is that the welding person using the machine does not require great skill, that is, it is a technique that can be learned more quickly than others.
Fast welds, same quality. Laser welding allows fast welding of different materials without losing any quality. The result is very satisfactory and resistant, clean, aesthetic and durable welds are obtained.
Versatility. With the same laser machine we can easily weld different types of materials: aluminum, copper, steel, plastics, among other options. In the same way, we can choose whether to weld with or without the addition of material.
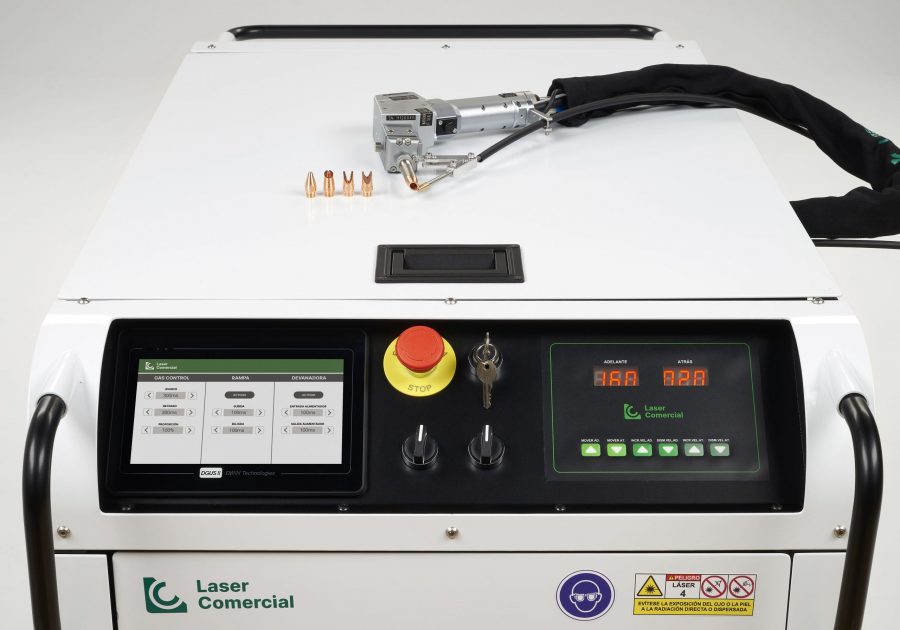
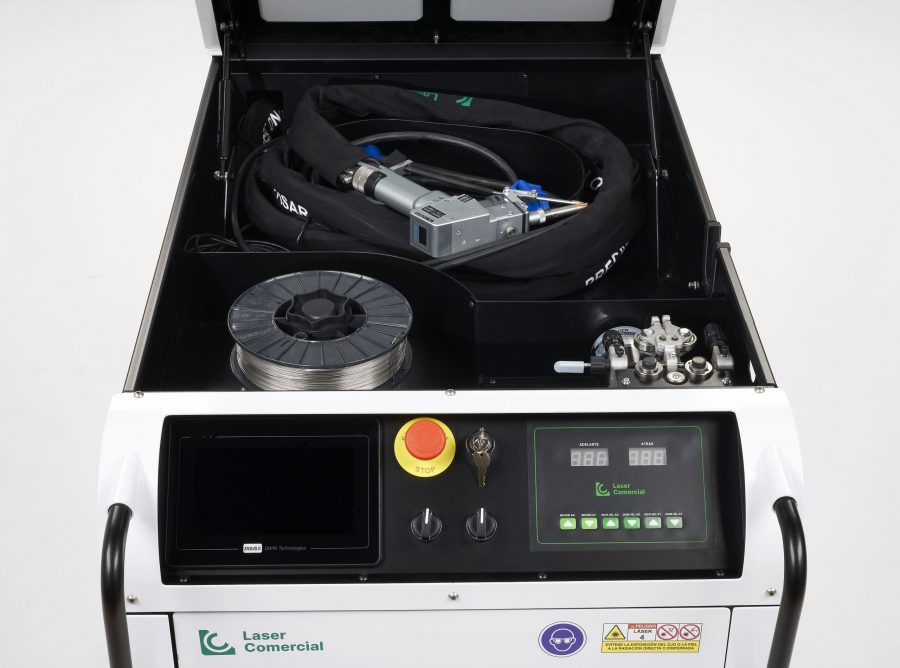
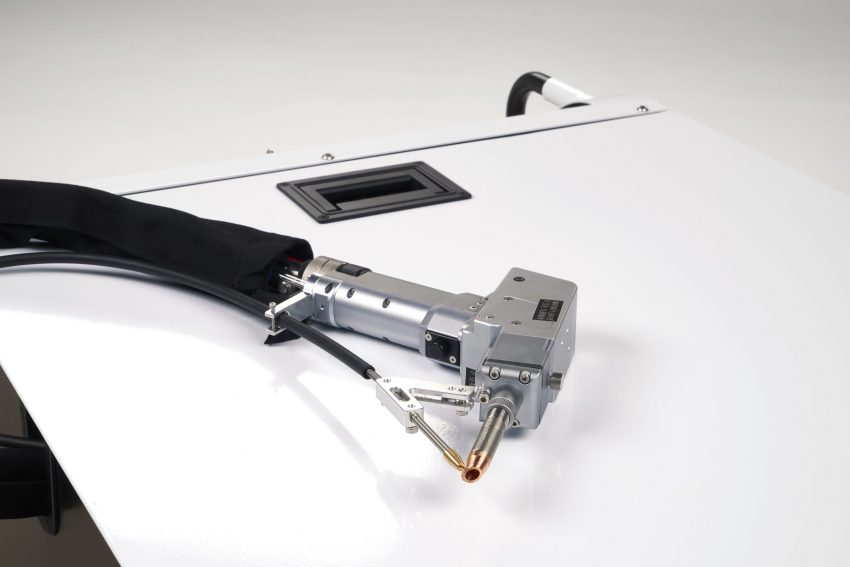