This website uses cookies so that we can provide you with the best user experience possible. Cookie information is stored in your browser and performs functions such as recognising you when you return to our website and helping our team to understand which sections of the website you find most interesting and useful.
Automotive Parts Marking: Precision and Efficiency with LC LASERS Technology
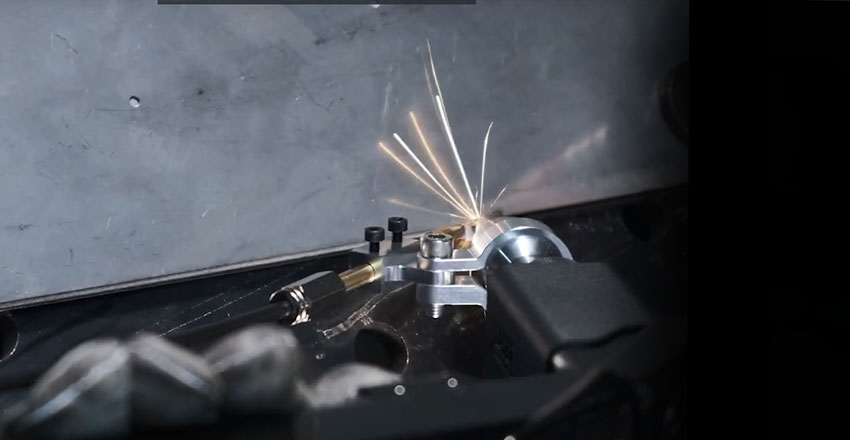
Summary:
Laser welding technology is making a significant impact in the automotive sector, particularly in the marking process for parts, where manufacturers constantly strive to enhance precision and efficiency.
In this article, we will explore how this technology has evolved, the specific benefits it brings to the sector, its most notable applications, and the future of laser welding in automotive manufacturing.
If you still have questions after reading, feel free to reach out to us via our web form, and a laser welding specialist will contact you to address any concerns.
What is Parts Marking?
Parts marking is a key process in the automotive industry, enabling metal parts to be joined through small weld points to ensure the structural strength and safety of vehicle components. These weld points are essential for assembling various parts of the automobile, from the chassis to the bodywork, ensuring they stay securely joined and can withstand the extreme conditions a vehicle faces in operation.
Traditionally, this marking was done using resistance welding, a method that applied pressure and electric current between electrodes on metal parts, generating heat to fuse the surfaces together. Although this technique was the standard for a long time, it had certain drawbacks. The application of heat and pressure could cause deformations or imperfections, affecting the quality of the joints and, consequently, the performance of the parts. Moreover, control over this process was limited, and the desired level of precision was not always achievable.
Laser welding, however, offers a revolutionary alternative. Instead of applying pressure and electric current, this technology uses a focused light beam, which allows materials to be melted and joined with millimeter precision. This precision enables the creation of finer and more exact joints, eliminating deformations and ensuring that the assembled components are more durable. Additionally, the speed of laser welding reduces production time and results in a consistent, high-quality finish.
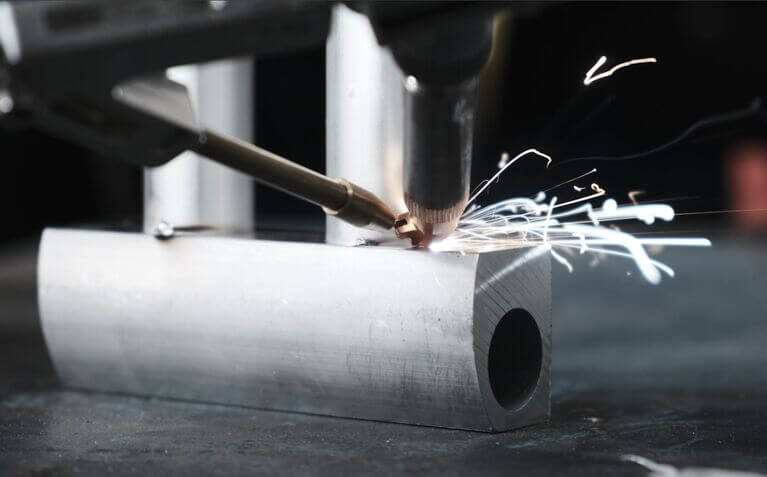
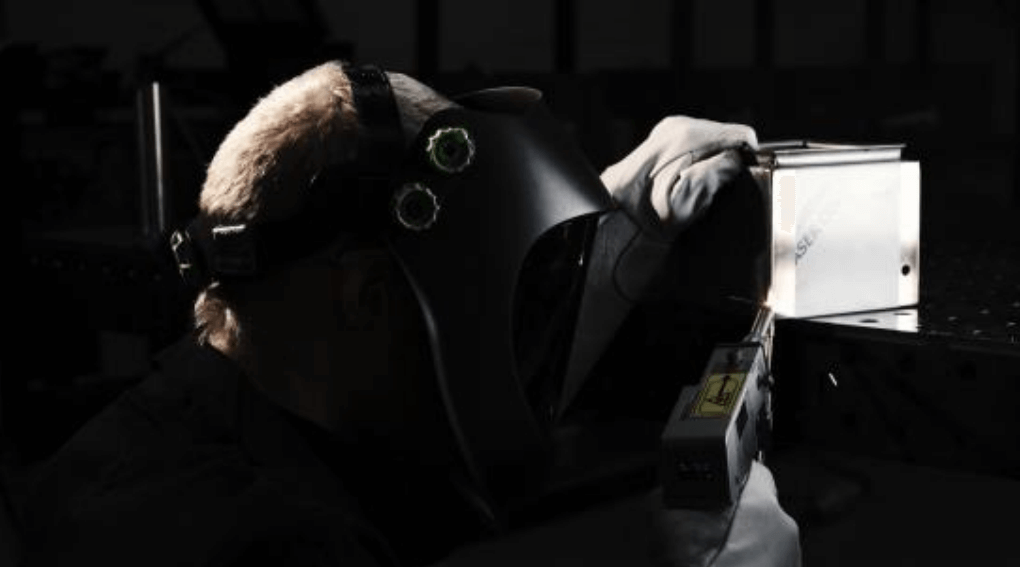
Advantages of Marking with Laser Welding Technology
Marking with laser welding technology offers a range of benefits that make it a preferred choice over traditional methods:
-
Enhanced Precision and Control: The ability to control a laser beam enables extremely fine and precise weld points. This significantly reduces the risk of deformations, as the laser only affects the necessary areas without impacting the surroundings. In the automotive industry, where every millimeter matters in the fitting and assembly of parts, this level of precision is invaluable.
-
Increased Speed and Efficiency: Compared to other methods, laser welding is much faster, allowing for a greater number of weld points to be completed in less time. This not only improves production line efficiency but also helps reduce operating costs. Faster processing translates to higher production capacity and reduced delivery times.
-
Lower Heat Input: Laser welding generates significantly less heat than other welding methods, which reduces the risk of thermal damage to the parts and adjacent materials. This is especially important in the automotive industry, where the structural integrity and durability of components are crucial.
-
Reduction of Defects and Errors: Since laser technology offers extremely precise control, errors and defects in the welds are minimized. This means that parts assembled with laser welding maintain high quality and consistency, leading to fewer repairs and less wear in the vehicle’s daily use.
-
Compatibility with Advanced Materials: Laser welding is compatible with a wide range of materials, including some of the most advanced in the industry, such as high-strength steels and lightweight alloys. This is essential in modern automotive manufacturing, where optimizing weight without compromising safety is a priority.
The Future of Automotive Parts Marking with Laser Welding
At LC LASERS, laser welding technology continues to evolve and improve. In the coming years, this technology is expected to be even more integrated with automation, enabling real-time control and monitoring of welding parameters. This combination of laser welding with advanced technologies will allow for automatic error detection and correction, ensuring final product quality while reducing inspection and quality testing times.
Additionally, research into new materials and special alloys is also driving the adoption of laser welding, as this technology provides an adaptability unmatched by other methods. Over time, the costs of implementing laser welding are expected to decrease, making it accessible to a greater number of manufacturers and expanding its applications in the industry.
At LC LASERS, we are transforming automotive parts marking by offering unprecedented precision, speed, and durability. As automation technologies and advanced materials continue to evolve, laser welding promises to keep revolutionizing automotive manufacturing, optimizing efficiency, enhancing vehicle quality, and meeting the demands of an ever-changing industry.