This website uses cookies so that we can provide you with the best user experience possible. Cookie information is stored in your browser and performs functions such as recognising you when you return to our website and helping our team to understand which sections of the website you find most interesting and useful.
Is laser welding suitable for high-precision work?
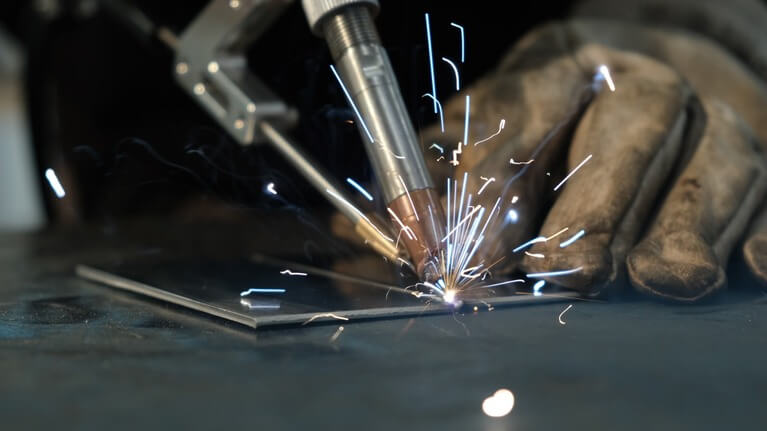
The Laser Welding We Want
In an increasingly demanding industrial world—where quality, speed, and precision are key—advanced joining technologies have taken center stage. In this context, industrial laser welding has become one of the best options for achieving precise, clean, and strong joints.But is it really suitable for high-precision work? At LC LASERS, specialists in laser solutions for the industry, we explore this key question.
What Is Laser Welding?
Laser welding is a thermal joining process that uses a high-intensity beam of light to melt the edges of two metal parts, allowing them to be joined with great accuracy. This beam, concentrated on a very small point, offers exceptional control over the weld zone. Unlike traditional methods, it does not require physical contact with the material, which significantly reduces equipment wear and improves process repeatability.
It is a versatile, precise, and high-performance technology, making it ideal for tasks where detail matters. That’s why more and more companies are incorporating laser welding machines into their production lines to optimize results and stay competitive.
Key Advantages of Laser Welding in High-Precision Work
Laser welding stands out from other techniques due to its level of control, speed, and quality of finish. Here are its main advantages:
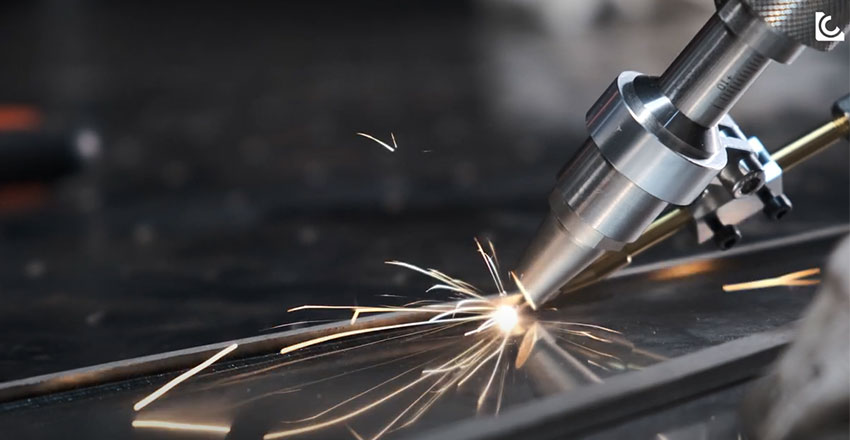
1. Extreme Precision
The laser beam can focus on a point just a few microns wide, allowing precision welding even on very small or delicate components. This is especially useful in applications where there is no margin for error.
2. Low Thermal Impact
Unlike other welding techniques, the laser welding machine concentrates heat only on the exact joining area, avoiding thermal damage to surrounding zones. This is vital when working with sensitive materials or thin parts.
3. High Speed and Efficiency
The laser process can perform welds in fractions of a second, reducing production times and increasing efficiency in automated industrial environments. It also integrates easily with robotic systems.
4. Clean and Professional Finish
Laser welding results in a fine, uniform, and clean weld seam that usually requires no rework or polishing. This translates into time savings and improved product aesthetics.
5. Adaptability to Different Material
Laser welding machines can work with a wide range of metals: stainless steel, aluminum, copper, titanium, brass, and others. This makes them ideal for diverse or complex production environments.
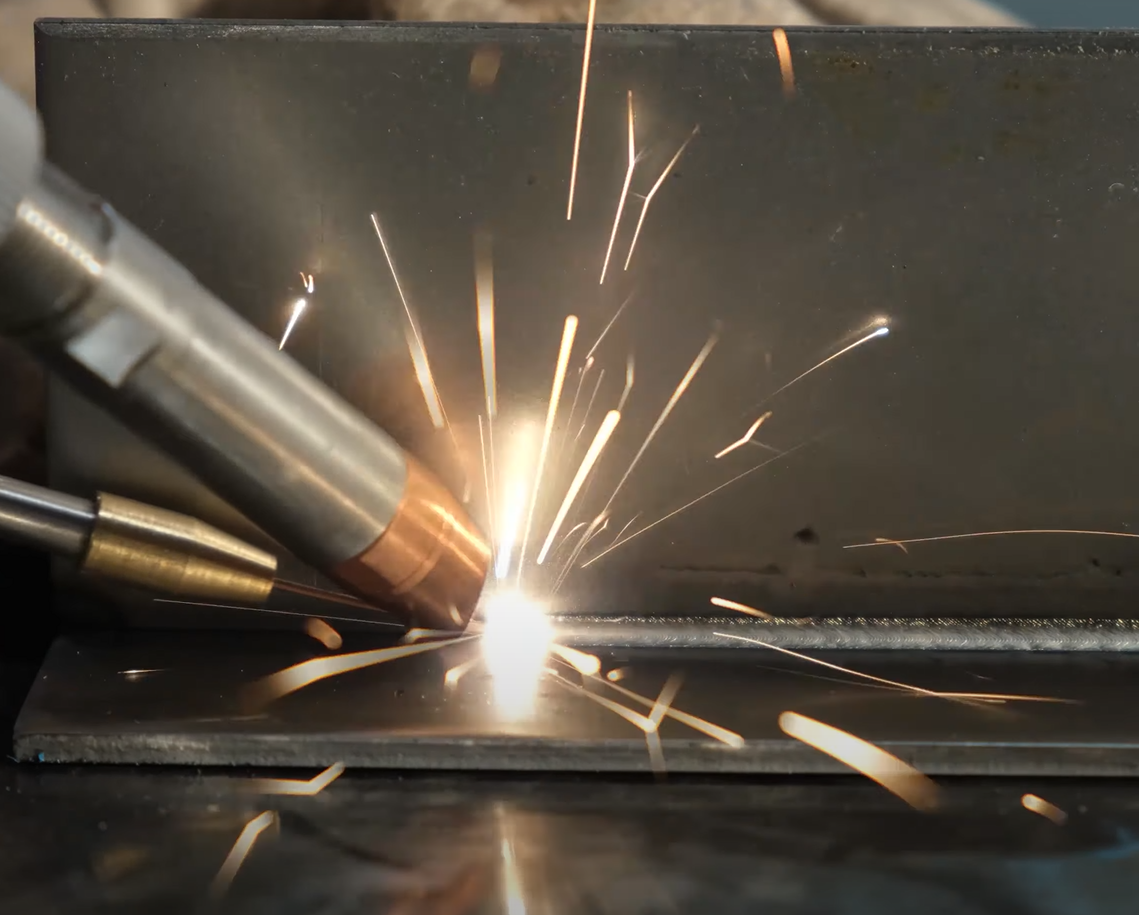
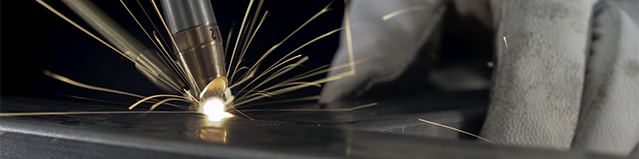
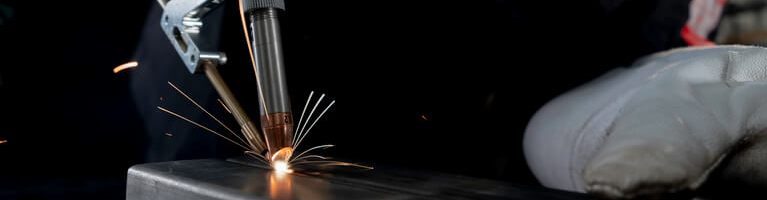
How Does Laser Welding Help in Demanding High-Precision Industrial Applications?
Many industries face similar challenges: improving product quality, reducing manufacturing time, minimizing error margins, and optimizing resources. In this sense, industrial laser welding provides concrete solutions in various sectors:
-
Precision in small components: Ideal for tiny parts where other technologies fall short without compromising structure or function.
-
Weight reduction in complex structures: In automotive or aerospace industries, laser welding allows for lighter designs without sacrificing strength.
-
Improved productivity: High welding speed increases output without losing quality, even in technically demanding parts.
-
Reduced human error: Automation with laser systems significantly reduces defects and inconsistencies.
-
Consistent quality in large volumes: In mass production, laser welding ensures a constant quality level that's hard to match with manual or traditional methods.
Whether it's for medical devices, electronic microcomponents, or complex metal structures, laser welding provides a clear competitive edge.
Why Our 3 Laser Welding Machines Are Perfect for Your Business
At LC LASERS, we offer three models of laser welding machines: SMART, PRO, and NEO. Each is designed to meet different industrial needs—from compact, versatile setups to high-power solutions for long production runs. While each machine offers unique benefits, they all deliver one essential feature: precise, clean, and efficient welding.
LC-WELD SMART
Compact, practical, and efficient. Perfect for work in tight spaces or when mobility is required—without sacrificing quality or precision.
LC-WELD PRO
Powerful and versatile. Ideal for demanding production where high speed, minimal thermal input, and constant performance are needed.
LC-WELD NEO
Our most advanced option. Equipped with next-gen technology and designed to offer maximum ergonomics, efficiency, and stability during long working sessions.
All our machines share the following advantages:
-
Intuitive and easy-to-program interface: Simplifies operation and reduces staff training time.
-
High durability and low maintenance: Built with high-quality materials for long life and minimal upkeep.
-
Consistent and professional results: Ensures high-quality welds with minimal deformation and excellent finishing.
-
Specialized technical support and customized training: We provide tailored technical assistance and training to meet each client’s needs.
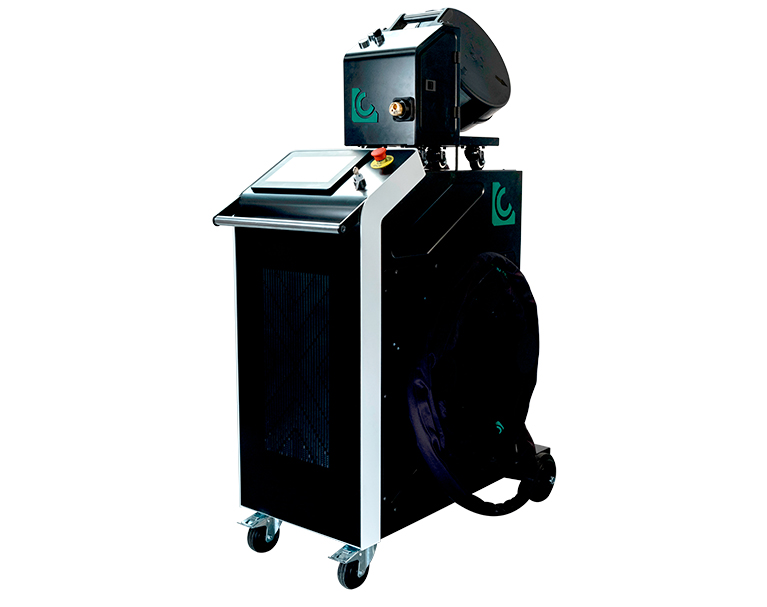
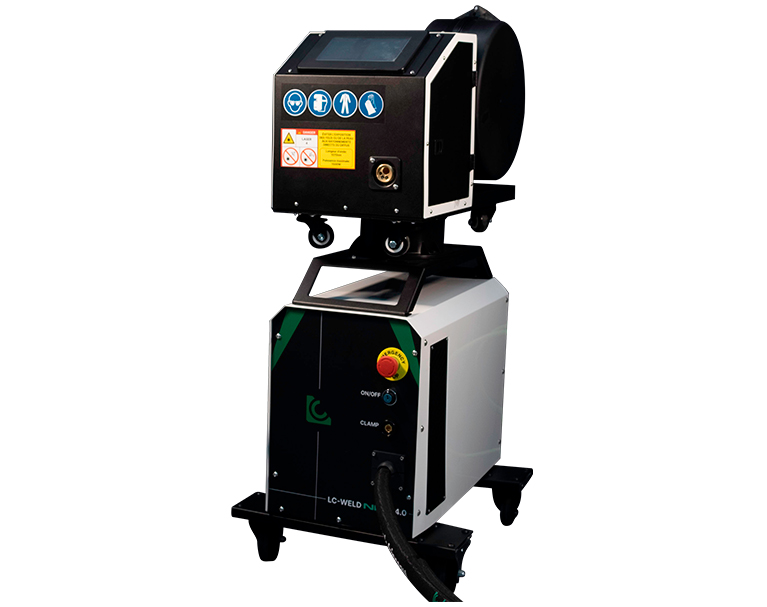
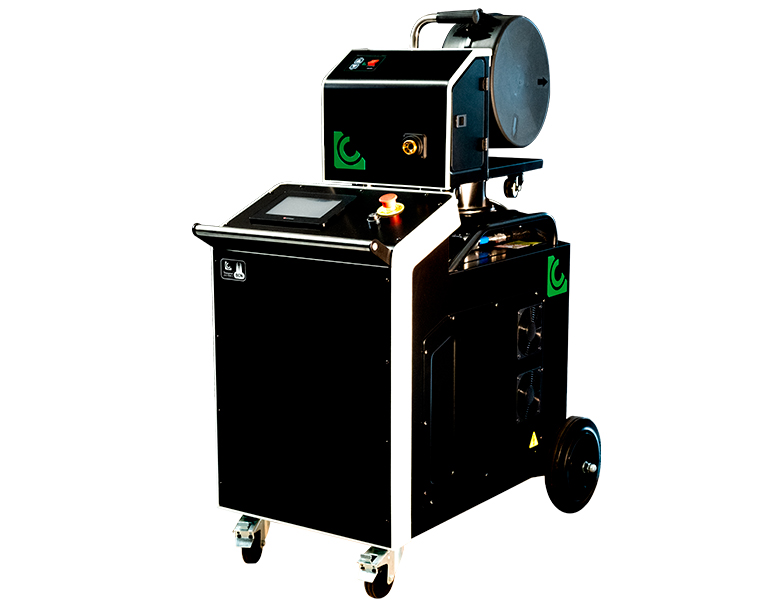
Laser welding is not only suitable for high-precision work—it’s the ideal solution for industries that demand accuracy, cleanliness, speed, and reliability. From tiny components to complex structures, this technology has become a pillar of industrial innovation.
At LC LASERS, we don’t just offer laser welding machines; we offer solutions designed to improve your results, reduce costs, and take your production to the next level. Are you ready to take the leap into precision?
Contact us and discover how we can help your business with the most advanced laser technology on the market.