This website uses cookies so that we can provide you with the best user experience possible. Cookie information is stored in your browser and performs functions such as recognising you when you return to our website and helping our team to understand which sections of the website you find most interesting and useful.
Laser cleaning of plate heat exchangers
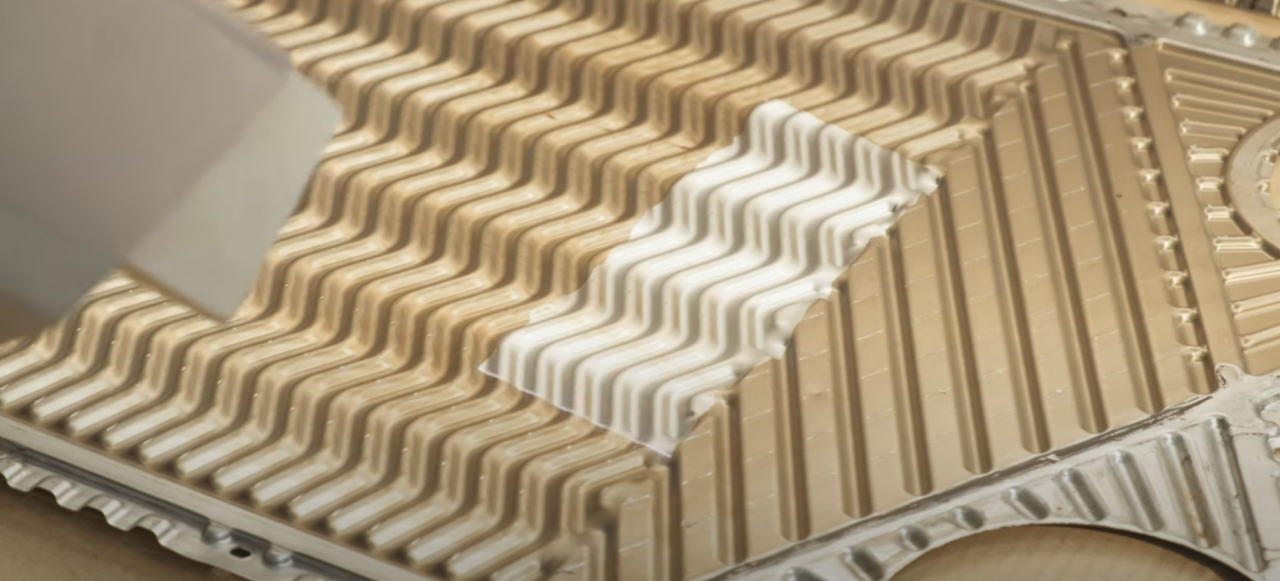
Summary:
Indirect heat exchangers are classified into several types, of which they can be: plate, shell and tube, spiral, among others. Usually, the type of plate is the most prominent, because it offers an excellent solution to thermal problems. Plate heat exchangers consist of a specific grouping of corrugated metal plates with passage holes for the two fluids.
It is a special type of heat exchanger made to use metal plates placed in parallel. The placement of the plates is such that each plate simulates the shape of a channel. They are used in conventional heating and cooling technology or renewable energy. It can be added that they are also often used for the production of hot water. These devices have proven to be fragile enough to require a cleaning method that meets these types of requirements. LaserComercial offers laser cleaning machines, an innovative system that is characterized by effectively cleaning all kinds of impurities or damage caused by corrosion without damaging the substrate.
Advantages of applying laser cleaning to plate heat exchangers:
Laser cleaning machines offer us numerous advantages and benefits compared to other conventional alternatives ,which makes them one of the most viable options for this type of work. This laser cleaning system allows us to reduce electrical consumption , increase the speed of the processes and ensures the integrity of the heat exchanger plates. Laser cleaning machines allow us to clean on different materials leaving the material intact. That is, it allows us to remove rust, paint, coatings, dirt accumulated over time, grease, etc. This laser cleaning systemit is very easy to install, control and implement and at the same time they allow us to carry out a very precise and contactless cleaning.
Laser cleaning machines are perfect for all types of surfaces, they clean quickly while respecting the environment. These equipment have a laser of up to 100,000 hours of useful life. This technology is the newest development in the area of rust removal. Quickly cleans all types of metals at incredible speed. It has a comfortable and easy to use laser gun. This laser machine has a built-in control that allows you to set the speed, the shape of the laser output or the width of the beam. In this way, it is possible to adapt the machine to each job to be carried out, in addition to being able to save parameters for future occasions in a very simple way. It is a safe and effective process, applicable to many industries.
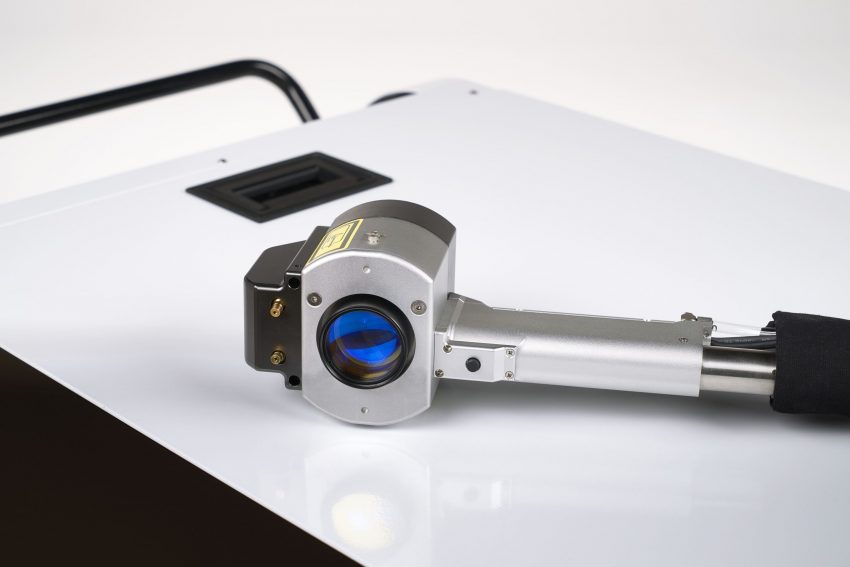
Types of laser cleaning machines:
At LaserComercial we have machines of different powers. To distinguish laser cleaning equipment we can classify them into 140W, 200W and 500W machines. After knowing their respective characteristics, each user who wishes to acquire a laser cleaning machine will make his decision based on his needs. In other words, what will make us say about choosing between a machine of a certain power or another is: the amount of dirt that we want to remove, the material on which we will work, the type of dirt or impurity that we need to clean, among other aspects. Similar. It is noteworthy that, being configurable equipment, a high power machine could work as a lower power one with the appropriate configuration.
140W Laser Cleaning Machine. They are ideal for removing light layers of oxide from small surfaces, rubber surfaces, some types of historic restorations, and stripping in small areas. In short, it would be the lowest cost equipment and a good option for not very large layers of dirt.
200W Laser Cleaning Machine. As we have highlighted, they are highly configurable equipment. They are high precision and efficiency equipment. These equipments are very suitable for applications such as: cleaning of medium dirt that do not require very high power, cleaning of welds or preparation of materials before being welded, historical restoration, removing layers of paint (depending on their thickness and encrustation), among others. Applications.
500W Laser Cleaning Machine . They are a very powerful option that can perform a very deep cleaning. They are widely used in metals to remove large amounts of rust, corrosion or coatings of all kinds, their applications are many due to their great possibility of configuration through a touch screen. Other applications to highlight would be: deep cleaning of machinery that has been outdoors for a long time or that accumulates large amounts of embedded dirt, remove corrosion, weld pre-treatment, among others.
Conventional alternatives to laser cleaning:
Currently there is a variety of alternatives for laser cleaning that have been used over the years for cleaning surfaces, but as the name says, they are conventional alternatives which can be improved, some of these alternatives manage to remove impurities or corrosion of the substrate, but at the same time they generate waste or generate toxic substances that can affect the operator. There are also methods that, due to the use of consumables, generate a high cost for the company. Due to all these circumstances, LaserComercial offers you laser cleaning technology that, as we saw in the section on its advantages, is the best alternative on the market.
Chemical cleaning. Chemicals pollute the environment and, in addition, waste must be managed. The chemical cleaning operation is more complex than the laser. The truth is that using chemicals we can damage the material, with the laser this does not happen.
Dry ice. It is a deep cleaning technique that is used in some industries. It consists of using grains of dry ice (co2 in solid state) to make them impact against a material with contaminants and dirt in order to clean the impurities. Inaccurate process and more complex operability than laser. It should also be taken into account that it is a process that the user must protect the body very well, a protective suit, helmet, glasses and hearing protection is essential to work with dry ice.
Blast cleaning . Cleaning technique that removes dirt through the impact of abrasive particles propelled towards metallic and non-metallic surfaces, but it has some drawbacks, such as, for example, the need for a large workforce in the different stages of the manual process.
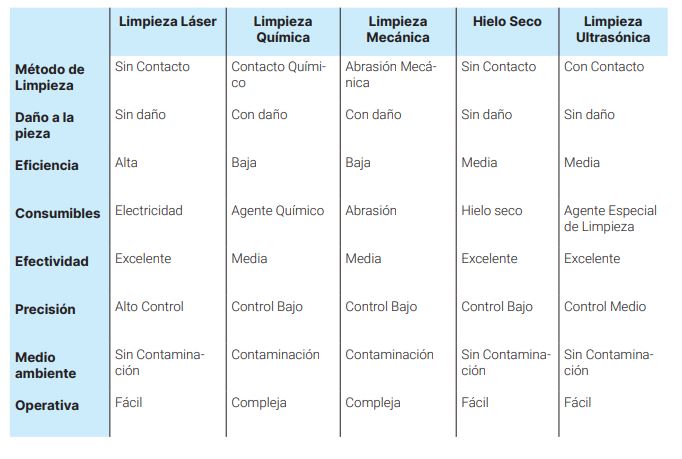