This website uses cookies so that we can provide you with the best user experience possible. Cookie information is stored in your browser and performs functions such as recognising you when you return to our website and helping our team to understand which sections of the website you find most interesting and useful.
What Makes Laser Welding Different? Everything You Need to Know
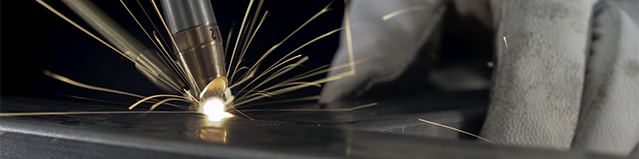
In the world of industrial welding, innovation is advancing rapidly, and one technology making a significant impact is laser welding. At LC LASERS, we are leaders in implementing cutting-edge laser welding machines designed to transform processes across industries such as automotive, electronics, jewelry, and more. With our expertise and technology, we provide solutions that stand out for their precision, speed, and versatility. But what makes this technique so special? In this blog, we’ll explore the advantages, applications, and reasons why laser welding is the best choice for your business..
What is Laser Welding?
Laser welding uses a concentrated laser beam as a heat source to join materials with extreme precision. Unlike traditional methods, this process minimizes thermal impact on parts and enables complex joints in delicate or high-strength materials.
Key Benefits:
- Precision: Delivers accurate welds, even in small or intricate areas.
- Speed: Improves efficiency compared to techniques like TIG or MIG welding.
- Versatility: Suitable for a wide range of materials, from stainless steel to precious metals.
- Quality: Produces strong and aesthetically pleasing welds, perfect for industrial and decorative applications.
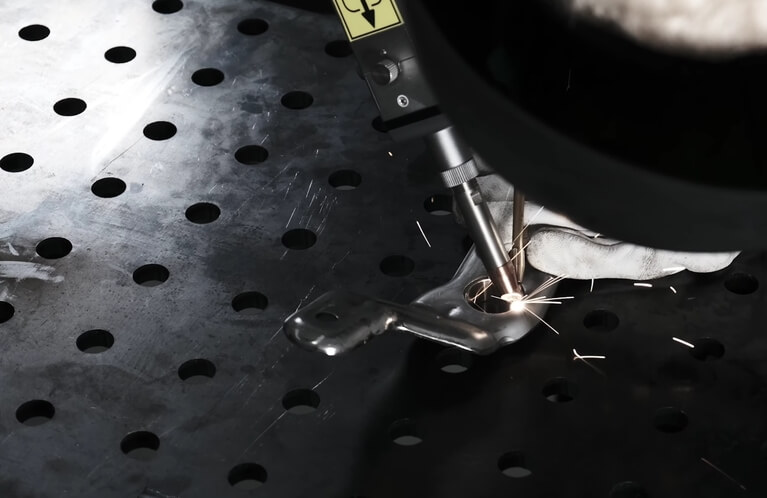
What Makes Laser Welding Different from Traditional Methods?
1. Reduced Heat-Affected Zone (HAZ):
Unlike conventional processes, a laser welding machine focuses heat on a small area, reducing deformation and improving precision for delicate materials.
2. No Need for Filler Materials:
Many laser welding applications do not require additional materials such as wires, reducing costs and ensuring a cleaner process.
3. Faster and More Efficient Welds:
The laser's speed allows jobs to be completed in less time, boosting productivity in industrial welding environments.
4. Automated Control:
Laser welding machines easily integrate into automated production lines, optimizing repeatability and reducing error margins.
5. Flawless Finishes:
Welds are smooth and aesthetically appealing, eliminating the need for additional finishing processes.
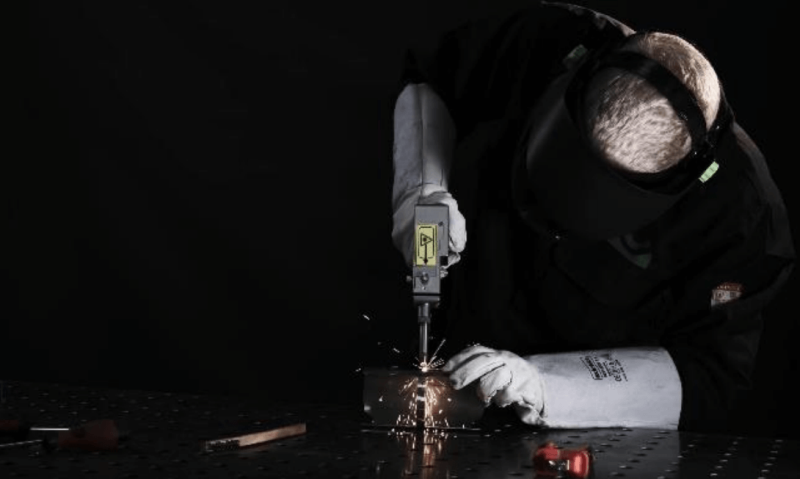
Key Applications of Laser Welding
-
Automotive Industry:
Joining complex parts in chassis, electronic components, and exhaust systems, ensuring high durability. -
Electronics:
Assembly of circuits and casings with precision, without affecting heat-sensitive components. -
Jewelry and Watchmaking:
Repairing and creating intricate designs in precious metals like gold and silver. -
Medical Sector:
Manufacturing medical devices and surgical instruments with clean and sterile welds. -
Aerospace:
Welding critical components in engines and fuselages requiring maximum strength and precision.
Comparison Between Laser Welding and Traditional Methods
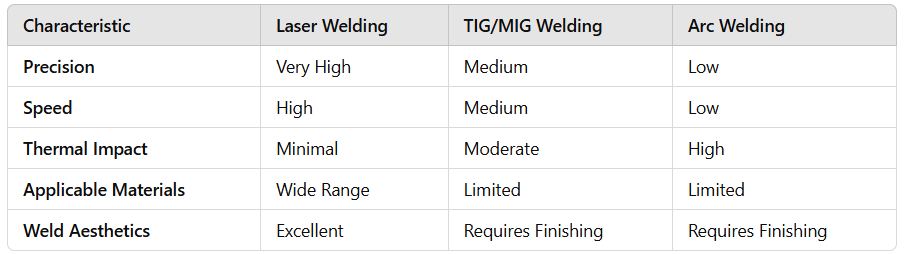
Laser welding is a technology that combines speed, precision, and versatility, offering unmatched benefits over traditional industrial welding methods. Laser welding machines not only improve productivity but also ensure superior quality finishes, ideal for the most demanding industrial settings.
At LC LASERS, we specialize in implementing advanced laser technologies. If you’re looking to optimize your welding processes or explore the advantages of laser welding, contact us today. Our team is ready to help you transform your business.