This website uses cookies so that we can provide you with the best user experience possible. Cookie information is stored in your browser and performs functions such as recognising you when you return to our website and helping our team to understand which sections of the website you find most interesting and useful.
Laser welding prevents deformation in sensitive parts
Descubre cómo la soldadura láser está revolucionando la industria del acero con sus múltiples ventajas e innovaciones.
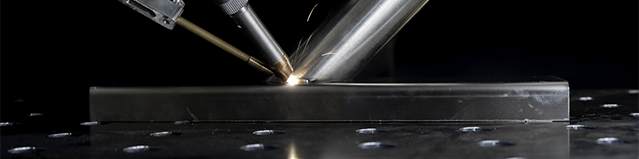
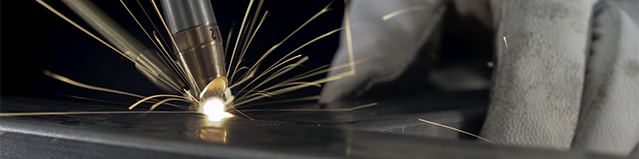
Laser welding
In modern industrial manufacturing, precision is not a luxury—it’s a necessity. In sectors such as electronics, aerospace, or medical device production, even the slightest deformation can ruin a part or compromise an entire system. In this context, laser welding has become the preferred solution for joining delicate parts without altering their geometry or material properties.
At LC LASERS, we specialize in offering industrial laser welding machines designed to deliver flawless results and tailored to the most demanding applications. Our expertise in precision welding positions us as leaders in laser solutions for industries where reliability is non-negotiable.
What is laser welding and how does it work?
Laser welding is a process that uses a high-powered laser beam to melt and join materials—usually metals—with extremely high precision. The heat is generated locally in a very small area, allowing for work with tight tolerances and minimal impact on surrounding material.
Laser welding machines can operate in automatic, semi-automatic, or manual modes, depending on the system and the application. At LC LASERS, we use cutting-edge technology that offers full control over the process: laser power, travel speed, beam diameter, and more.
This method is contactless, clean, fast, and precise. It can be used for spot welding or continuous seam welding, making it ideal for delicate or complex-shaped components.
Main Advantages of Laser Welding in Industry
The rise of industrial laser welding is no coincidence. It offers significant benefits over traditional welding methods like TIG, MIG, or resistance welding:
-
High precision: The laser can be focused on extremely small areas, resulting in fine, detailed welds without damaging the part.
-
Low thermal input: Because the heat is concentrated, thermal impact is minimized, preventing internal stresses and deformations.
-
Fast processing speed: Much faster than traditional methods, increasing productivity in industrial environments.
-
Aesthetic quality: Weld seams are clean and usually require no post-processing—ideal for industries such as jewelry or consumer tech.
-
Material flexibility: Suitable for welding stainless steel, titanium, aluminum, copper, and even dissimilar metals.
These features make the laser welding machine ideal for applications where precision matters more than brute strength.
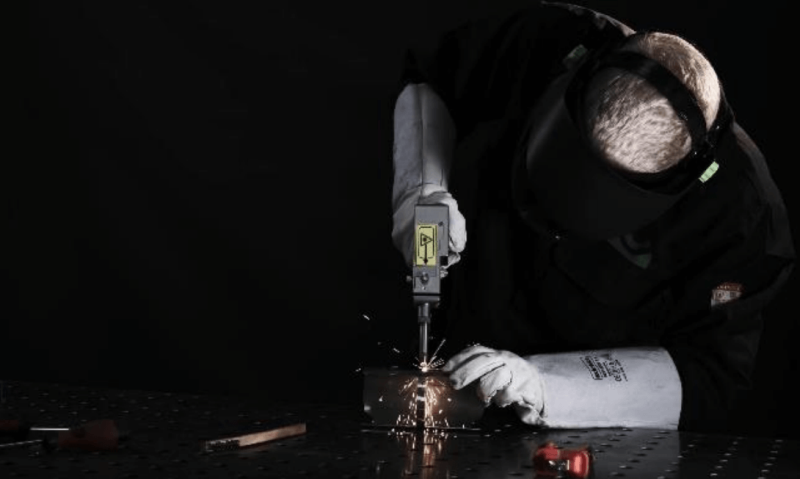
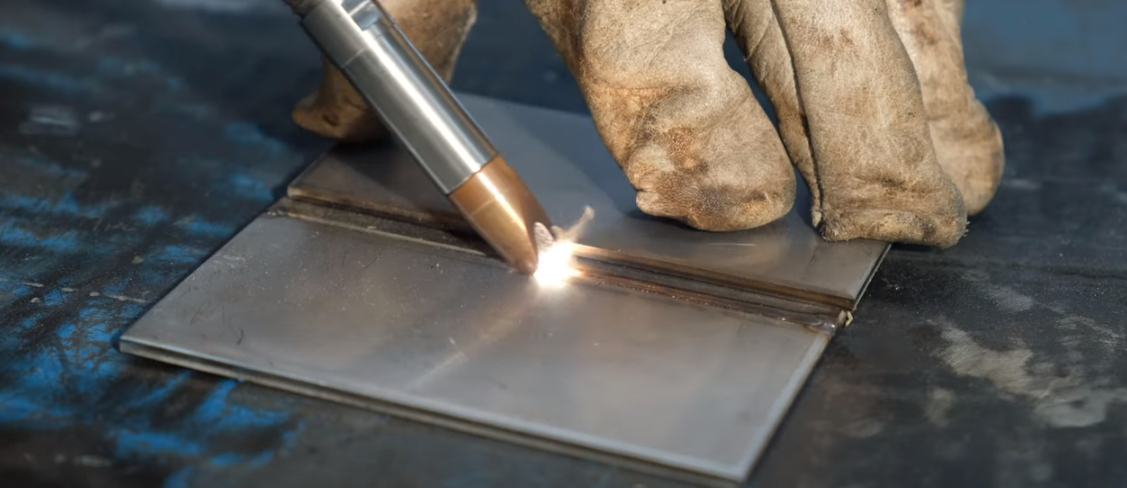
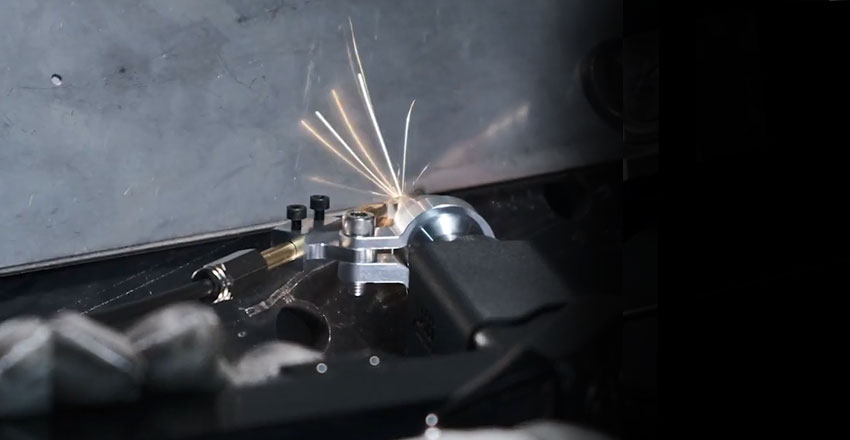
Deformations in Traditional Welding: Causes and Consequences
One of the biggest challenges of conventional welding is thermal control. Traditional methods apply large amounts of heat, causing expansion and contraction that leads to mechanical deformation.
The consequences of this deformation can be critical:
-
Loss of dimensional tolerances
-
Alteration of mechanical properties
-
Functional failure
-
Costly rework or part rejection
This is especially problematic in precision components or small production runs, where part loss is not acceptable.
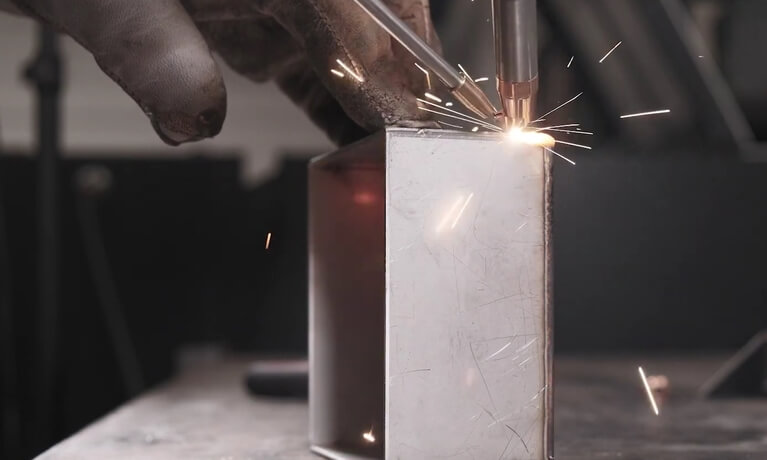
How laser welding prevents deformation
This is where laser welding truly shines. By concentrating the beam on a specific point, heat input is minimal and dissipates quickly. This prevents overheating of the surrounding area, significantly reducing the risk of distortion.
Additionally, precision laser welding enables:
-
Controlled pulses, further limiting heat input.
-
High speeds, minimizing heat transfer to the material.
-
Automated integration, ensuring consistent results every time.
In short, this process not only improves joint quality but also protects the structural integrity of the part.
Applications in sensitive industries
Laser welding machines are especially valued in sectors where precision is a top priority:
Aerospace Industry
In this sector, where every gram counts, the ability to join parts without affecting their structural properties is vital. Laser welding is ideal for components like engine parts, turbine blades, and lightweight structural frames.
Electronics and Microcomponents
Device miniaturization demands welding techniques that won’t damage circuits, connectors, or sensitive components. Laser welding’s non-contact nature is perfect for PCBs, sensors, and tiny electrical connections.
Medical and Dental Sectors
Implants, prosthetics, and surgical instruments require flawless surfaces and preserved material properties. Precision laser welding ensures hygienic, durable, certified results.
Jewelry and Watchmaking
These industries demand both precision and aesthetics. Laser welding enables virtually invisible seams with no burrs or burn marks—ideal for gold, silver, and stainless steel.
Laser welding machines offered by LC LASERS
At LC LASERS, we offer a comprehensive range of industrial laser welding machines tailored to your specific needs. Here’s a closer look at our top models:
1. LC-WELD SMART
An entry-level model designed for affordability and ease of use, perfect for small workshops and those entering the laser welding space. It delivers high-quality welds quickly and efficiently.
Best for:
-
Stainless steel welding
-
Jobs requiring fast, reliable welds
2. LC-WELD PRO
This is a next-generation 1500W machine built entirely by LC LASERS. It enables operators to work faster and more efficiently than with traditional methods, making it ideal for industries like automotive.
Best for:
-
Spot welding automotive parts
-
Leak-proof welds
-
Welding stainless steel with or without filler material
3. LC-WELD NEO
Our latest innovation, combining performance, quality, and ease of use in a compact design. Features a new LC-GUN V4.4 and a laser generator that is 42% more efficient.
Best for:
-
Welding cylindrical tubes
-
Internal/external corner welding
-
Multi-material applications
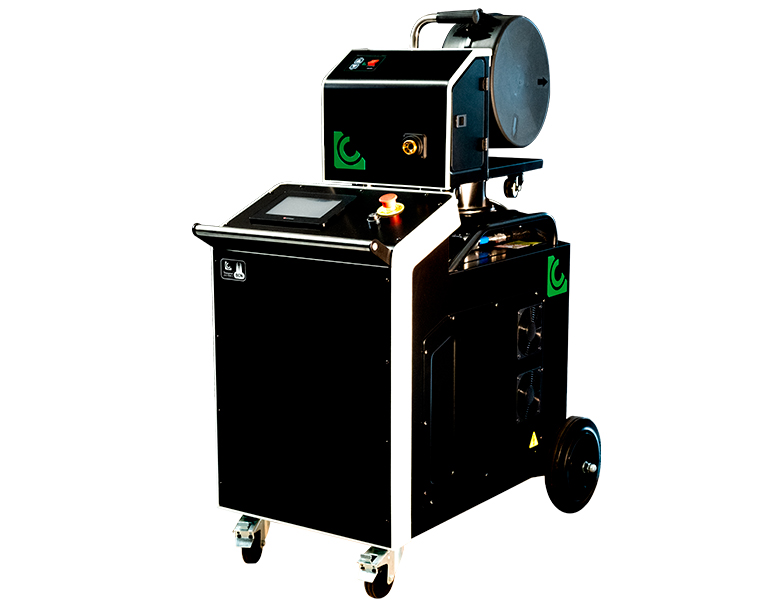
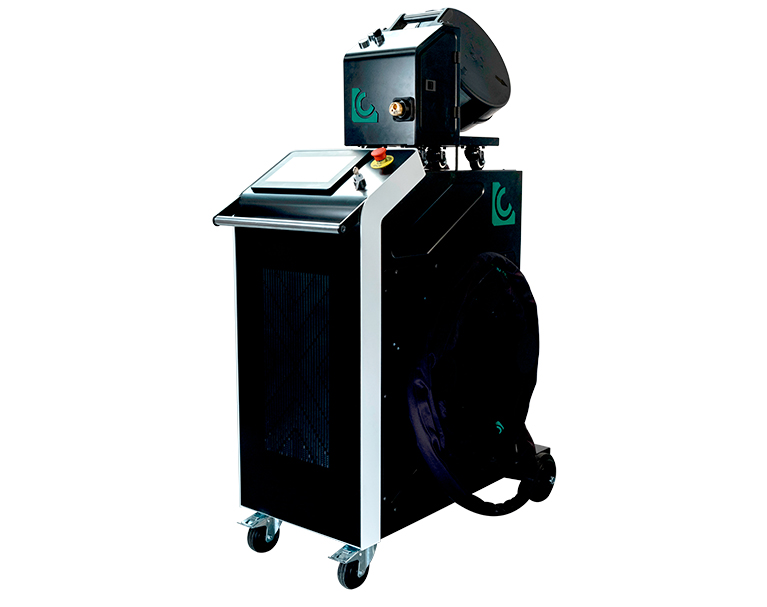
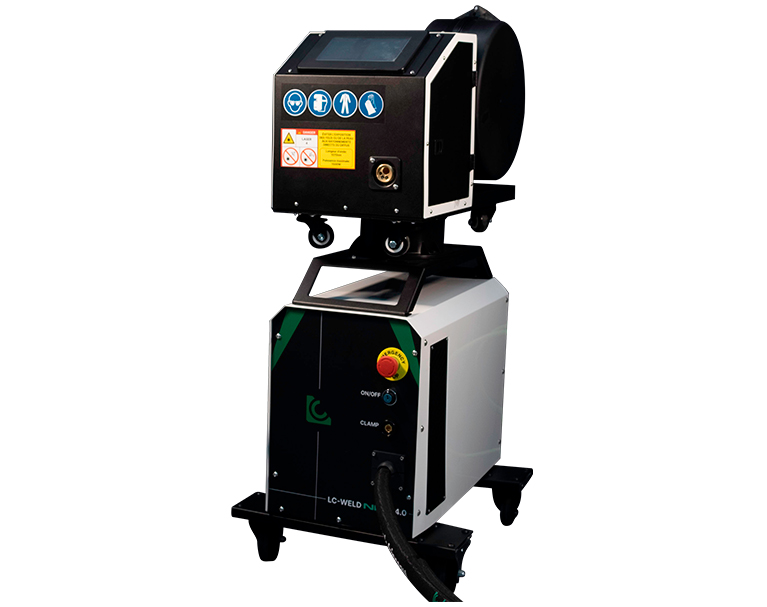
Conclusion
Industrial laser welding is not just a technological upgrade—it’s a manufacturing revolution. For companies working with sensitive parts where deformation is unacceptable, this technique offers unmatched control, precision, and efficiency.
At LC LASERS, we provide the exact solution you need. Whether it’s a high-volume production laser welding machine or a flexible tool for specialized tasks, our team is ready to help.
Want to improve your welding process and eliminate deformation in your most sensitive parts?
Visit https://lclasers.com, explore our solutions, or contact us directly for personalized advice.
Your production deserves maximum precision. Trust laser technology. Trust LC LASERS.