This website uses cookies so that we can provide you with the best user experience possible. Cookie information is stored in your browser and performs functions such as recognising you when you return to our website and helping our team to understand which sections of the website you find most interesting and useful.
Laser cleaning, an alternative to sandblasting
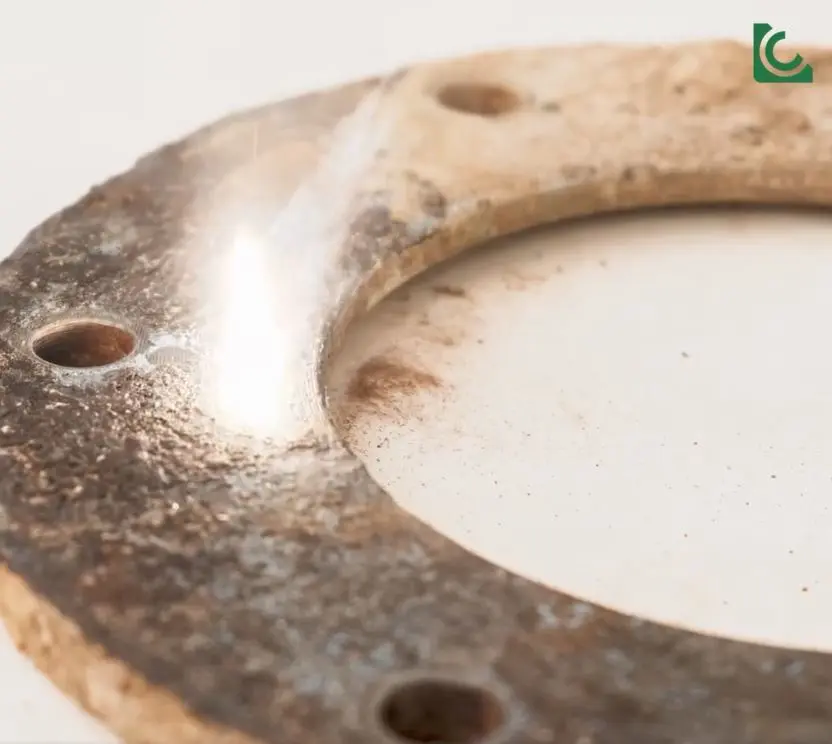
Summary:
In the industry there is a variety of techniques for cleaning surfaces such as facades or concrete objects. In this case we will talk about two: laser cleaning and sandblasting <<sandblasting>> . As we already know, laser cleaning is a method that does not require going through many security processes, because equipment such as LC-CLEAN is safe and easy to use, unlike the sandblasting system.
Sandblasting consists of projecting sand or an abrasive powder on the wall without adding water. This projection of abrasive material is used in particular on hard surfaces.
This method is involved in cases of silicosis, a serious lung disease. This is because the percentage of silica contained in the abrasives used in this process is very high.
Laser cleaning, main alternative to sandblasting
Sandblasting is a widely used technique in a variety of industries that involves removing all dirt and scale from the surface of an object with a high-speed abrasive medium. Sandblasting requires a more complicated and complex protection system, PPE sometimes uncomfortable for the user, after protection measures, because the abrasives used usually contain silica dust, which is harmful to health. . In countries such as France, this technique known as dry sandblasting is prohibited if the abrasive contains a proportion of silica greater than 5%. Considering that silica sand contains 90% or more.
On the other hand, laser cleaning does not use abrasives, which makes it a permitted technique in all countries, and above all the main alternative to sandblasting. The LC-CLEAN allows us, with a simple operation, to achieve the best cleaning results in a simple and safe way for the operator. This laser cleaning equipment is famous for being environmentally friendly by avoiding chemicals, corrosives or consumables. In addition, it does not generate large pollutants or waste that must be recycled in a specific way.
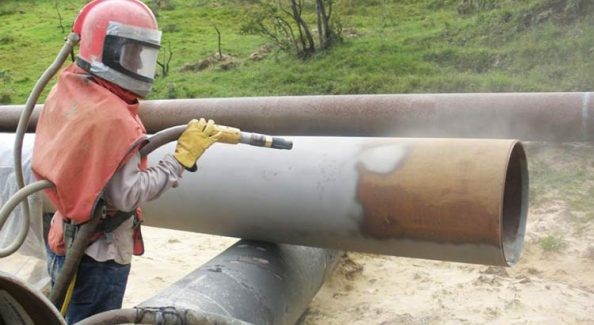
Laser cleaning, a safe and easy-to-use technique
Laser cleaning has revolutionized and replaced traditional cleaning and stripping systems, due to the fact that these techniques have their limitations and can cause damage and, in some cases, serious harm to the environment or to the people involved in the process. For this reason, laser cleaning systems have managed to improve many aspects of traditional cleaning systems in recent years.
Below, we mention some of these advantages of LC-CLEAN :
- Laser cleaning cleans dry, has no emissions and does not cause pollution. Waste can be recycled through filters and vacuum cleaners.
- Laser cleaning allows to effectively clean the surface and eliminate the absorption of submicron particles allowing better finishes.
- Laser equipment uses a fiber laser, which communicates via fiber optics. This makes it possible to achieve long-distance operation and thus be able to reach more complex areas and improve the safety of personnel working with this type of equipment.
- Thanks to the efficiency of laser cleaning, it allows us to save time and reduce costs in the long term. Save time, reduce costs.
- Laser equipment has good controllability, high flexibility, easy implementation, and high precision.
- The heat affected zone is small, with no thermal effect on the surrounding material, and no thermal damage. Laser cleaning is perfect for mold maintenance.
- Very low electricity consumption and very little maintenance.
Laser cleaning applications
The operation of the laser cleaning equipment is simple: it does not require a high technical level on the part of the operator, and it welds a wide variety of materials with the same technique, only changing the parameters of the equipment. It offers the operator great versatility.
Laser cleaning is the latest technology in deep and effective cleaning . With a highly concentrated fiber laser at a point, a process known as ablation is produced, which removes and removes impurities and dirt from different surfaces. There are many industries that are beginning to apply this technology in their day to day, since it is a very versatile and efficient technology. In addition, the piece is not damaged when using the laser, the substrate remains intact. It is a safe process for the user, which has good results.