This website uses cookies so that we can provide you with the best user experience possible. Cookie information is stored in your browser and performs functions such as recognising you when you return to our website and helping our team to understand which sections of the website you find most interesting and useful.
Laser Welding of Galvanized Steel
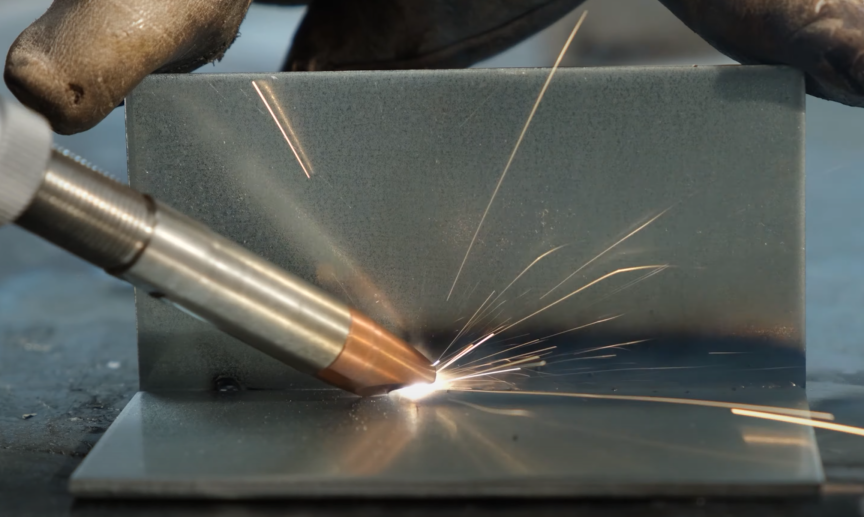
Summary
The main characteristic of GALVANIZED STEEL is the zinc coating that protects and makes it more beautiful. First of all, zinc does not rust and protects the steel from the oxidation process when in contact with air. In second place, less steel is consumed and when it is used less raw material is needed. Stronger and safer structures are built using less metal. In addition, galvanizing does not require long-term care and maintenance.
Of this type of steel, it stands out that it prevents corrosion, for that reason galvanized steel sheets are usually applied for the elaboration of electrical appliances, construction materials or structures. Of this type of steel, we can point out that it prevents corrosion, for that reason galvanized steel sheets are usually applied for the elaboration of electrical appliances, construction materials or structures. LASERCOMERCIAL brings you a solution for welding galvanized steel: using the laser welding technique .
Alternative traditional methods for laser welding of galvanized steel
For years, many industries has had different options for welding between two or more pieces. Like different industries, over the years it has undergone changes which has allowed the emergence of new alternatives such as laser welding . Which allows you to do the same function, but with different processes and with better results. Even so, many people or companies for reasons of distrust to innovate do not know or are in doubt as to which alternative is the correct or the most appropriate. That is why we will start by talking about the old techniques or methods that can perform the same function as laser welding, but with some disadvantages. There are techniques such as spot welding or arc welding that are usually applied to this type of material.
Spot Welding
This technique practically consists of heating one of the two parts to a temperature close to that of fusion and then applying pressure between them. This system works when the material is heated with electric current between two electrodes and it is these two that carry out the pressure of these two pieces. But during this process we can find the following inconveniences:
- The electrodes must be able to reach both sides of the connecting metal parts. Certain spot welders can only hold a certain thickness of metal, and while the position of the electrode can be adjusted, that limits movement in the electrode holders.
- The measurements of the electrode will determine the size and strength of the weld. Bonds only form where the metal and electrodes are in contact. If the current is not strong enough, not hot enough, or the metals are not bonded together enough, the weld may be small and weak.
- In the contour of the place where the spot welding has been carried out, deformations may occur. The corrosion resistance of the metal may also be affected, and an unsightly appearance may be formed because cracks may occur.
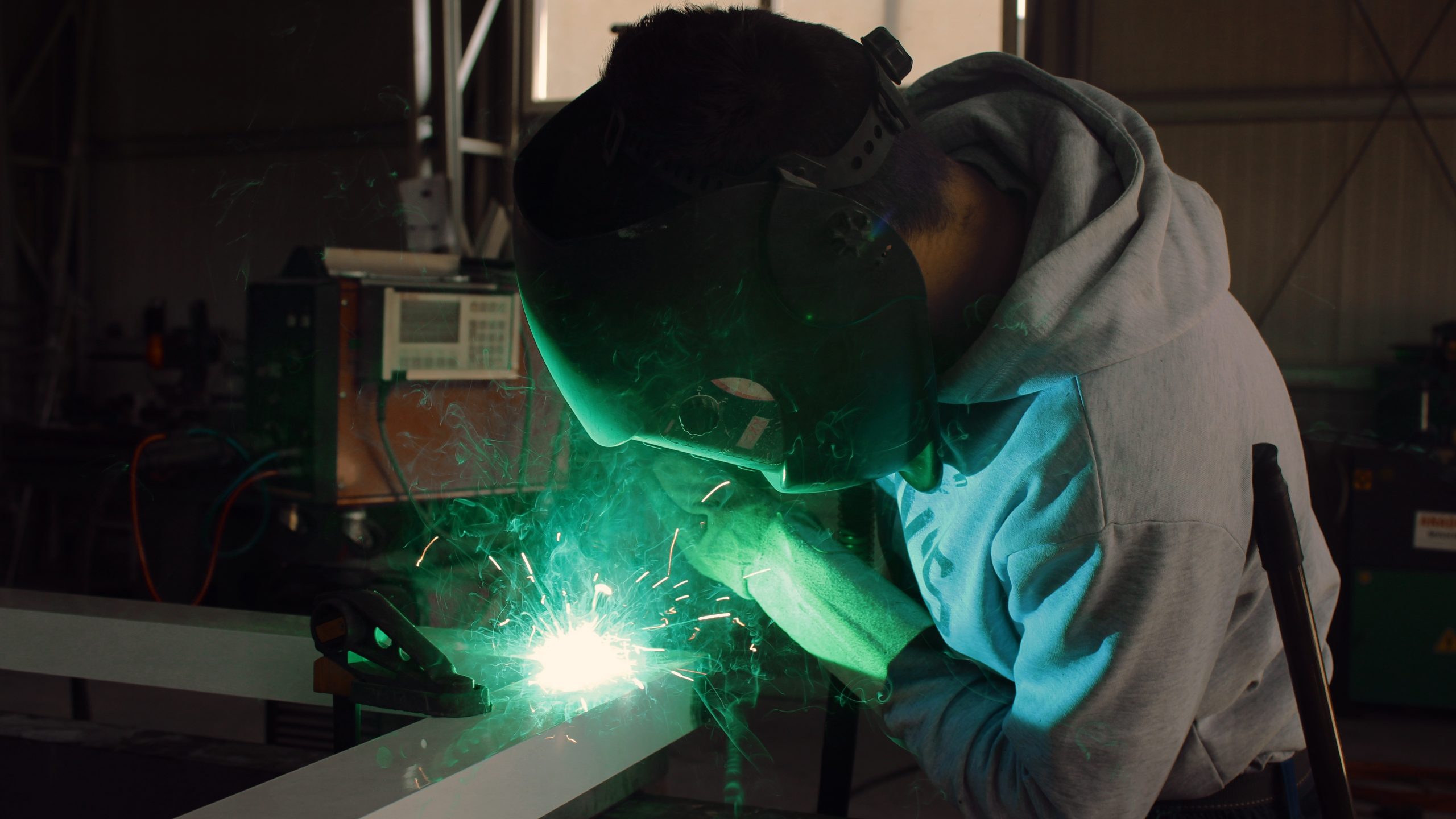
Arc welding
Fusion process whose function is the union of two or more metals forming the shape of an arc together with the electrode, hence the name. The pieces are placed at high temperatures through the use of a potential differential and intensity value of a determined electric current. As disadvantages when using arc welding we can highlight the following:
- The gases produced by the burning electrodes serve to protect the weld from oxygen. But it is these same gases such as chromium, manganese, nitrogen oxide and other heavy metals that work personnel breathe that cause short and long-term health damage.
- In order to apply this type of system, the work staff must have certain training and skills in the different processes involved in arc welding.
- It requires removing welding slag during and after the operation process and requires a high level of security measures against the high level of danger that this process can cause, such as individual protection equipment and for your surroundings. And it also does not allow for a smooth process or system due to the limited measurements of the electrodes.
Advantages of Laser Welding
- Provides fast , clean welding without discoloration and with few consumables.
- Being easy to use, this laser machine does not require a great deal of experience on the part of the welder than conventional welding equipment. It is enough to meet some very basic security requirements.
- Attractive design system with a control system with more ranges.
- Lightweight design, easy to use and manoeuvre, offering operator comfort.
- The different LASERCOMERCIAL models can reach up to 5mm of welding depth.
- We use a continuous wave (CW) laser that gives better results, compared to other lasers such as quasi-continuous (QCW) such as higher speed, less deformation, more depth, better finish.
- Automatic contribution, since it gives you the option of working with contribution through an automated thread feeding system .
- The precision of laser welding machines allows us to work very small and detailed seams.
- Laser machines allow you to save on different factors that other techniques would have cost you large sums of money such as expenses for electricity, operators, gas or filler material.
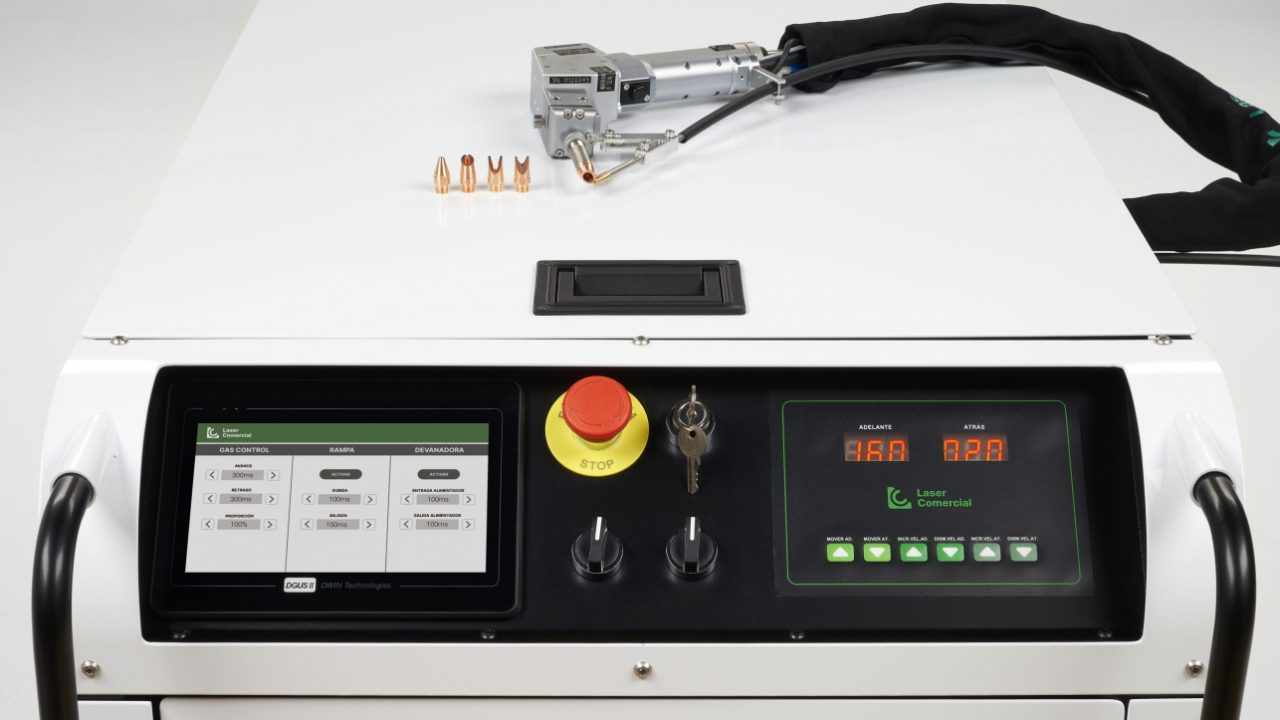
In conclusion:
In summary, we can conclude that the welding of galvanized steel using old or traditional welding alternatives can become a problematic process. The zinc coating melts at 450ºC and in doing so generates gases that create bubbles that create porosities and incorrect welds in poor condition. It requires a treatment of the metal and an almost obligatory contribution of material for the welding to be in good condition.
That is why laser welding is used as a method to cover the disadvantages of spot welding since it is not necessary to consider the dispersion of electricity.
To solve these problems and many more adversities that traditional welding methods pose, there is laser welding and LC-WELD equipment . LaserComercial’s laser welding represents a great innovation in the metal sector as it speeds up and makes the process very profitable, as well as improving the quality of the welds, leaving a fine and aesthetic welding line .
Laser welding is a fast method and does not require a great deal of experience to be used. It gives incredible results even on those metals that, with traditional methods, are more difficult to weld.